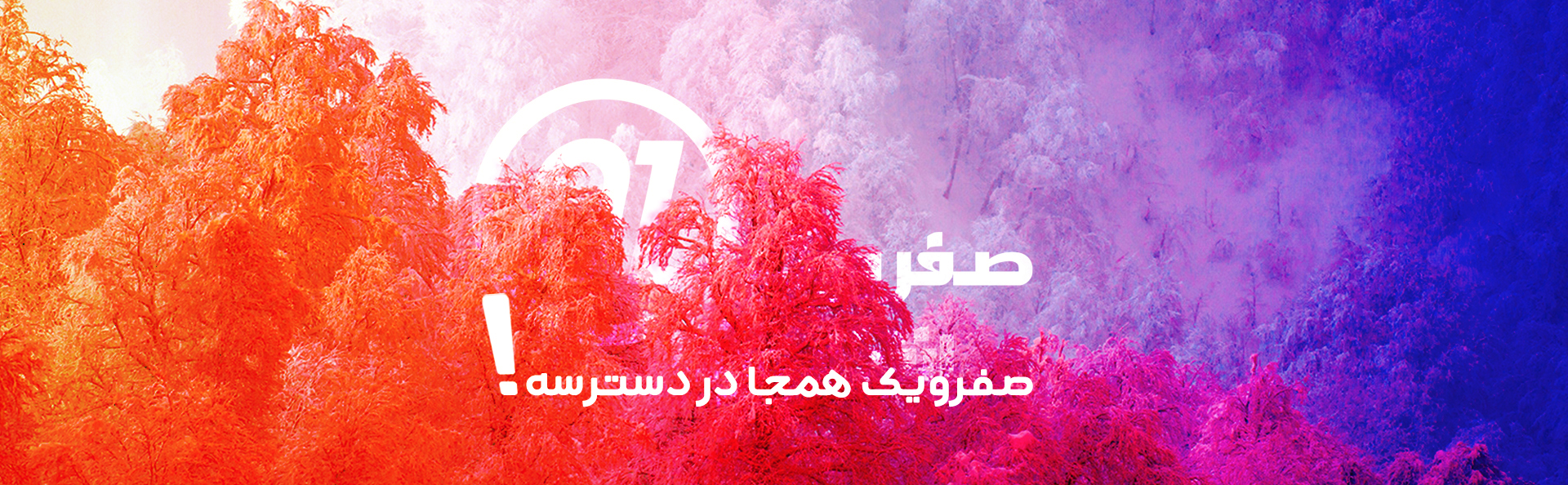
Gigacasting 2.0: انقلاب تسلا در خودرو سازی
Gigacasting 2.0: انقلاب تسلا در خودرو سازی
تسلا مجموعهای از نوآوریها را با هم ترکیب کرده است تا پیشرفتی در فناوری ایجاد کند که میتواند روش ساخت خودروهای الکتریکی را تغییر دهد و به ایلان ماسک کمک کند تا به هدف خود یعنی کاهش هزینههای تولید به نصف برسد. این شرکت پیشگام استفاده از پرس های بزرگ با فشار گیره بین 6000 تا 9000 تن برای قالب گیری ساختارهای جلو و عقب مدل Y خود در یک فرآیند “گیگاکستینگ” بود که هزینه های تولید را کاهش داد و رقبا را مجبور به تقلا برای جبران کرد.
به گفته مردم، تسلا در تلاشی برای گسترش برتری خود، به نوآوری نزدیک می شود که به آن امکان می دهد تقریباً تمام زیر بدنه پیچیده یک EV را به صورت یکپارچه به جای حدود 400 قطعه در یک خودروی معمولی، بسازد. منابع گفتند که دانش هسته اصلی استراتژی تولید «Unboxed» تسلا است که توسط مدیر اجرایی ماسک در ماه مارس رونمایی شد، و این یکی از محورهای برنامه او برای تولید دهها میلیون خودروی برقی ارزانتر در دهه آینده و همچنان کسب سود است.
تسلا گفته است که مدل Unboxed شامل تولید مجموعههای فرعی بزرگ از یک خودرو و سپس اتصال آنها به یکدیگر است، اندازه و ساختار بلوکهای مدولار هنوز موضوع حدس و گمان است. تری وویچوفسکی، رئیس شرکت مهندسی ایالات متحده Caresoft Global، گفت: اگر تسلا موفق شود قسمت اعظم زیر بدنه خودروهای الکتریکی را به صورت گیگا کاست کند، باعث اختلال بیشتر در نحوه طراحی و ساخت خودروها خواهد شد.
وویچوفسکی که بیش از سه دهه برای خودروساز آمریکایی GM (GM.N) کار میکرد، میگوید: «انجام ریختهگری بسیار سخت است، بهویژه قطعات بزرگتر و بزرگتر. پیچیده تر است.” دو منبع گفتند که طراحی و تکنیک های جدید قبلی گزارش نشده تسلا به این معنی است که این شرکت می تواند یک خودرو را از ابتدا در 18 تا 24 ماه توسعه دهد، در حالی که اینکار توسط اکثر رقبا در حال حاضر ممکن است بین سه تا چهار سال طول بکشد. وی گفت: یک قاب بزرگ – ترکیبی از بخشهای جلو و عقب با زیر بدنه میانی که باتری در آن قرار دارد – میتواند در خودروی الکتریکی کوچک تسلا استفاده شود که قصد دارد تا اواسط دهه با قیمتی معادل 25000 دلار روانه بازار شود.
چاپ سه بعدی و SAND
پیشرفت تسلا بر نحوه طراحی و آزمایش قالب های غول پیکر برای چنین قطعه بزرگی برای تولید انبوه تمرکز کرده است، و اینکه چگونه قالب های ریخته گری می توانند زیرفراب های توخالی با دنده های داخلی را برای کاهش وزن و افزایش قابلیت تصادف ترکیب کنند.
در هر دو مورد، نوآوری های توسعه یافته توسط این پنج متخصص اصلی: متخصصان طراحی و ریختهگری در بریتانیا، آلمان، ژاپن و ایالات متحده از چاپ سه بعدی و شن و ماسه صنعتی استفاده میکنند می باشد.
تا کنون، خودروسازان از ساختن سازه های بزرگتر به دلیل “معضل گیگاکست” خودداری کرده اند: ایجاد قالب برای ساخت قطعات 1.5 متر مربع در حین حال که کارایی را افزایش می دهد اما گران است و خطرات بی شماری را به همراه دارد.
به گفته یکی از متخصصان ریخته گری، هنگامی که یک قالب آزمایشی فلزی بزرگ ساخته شد، تغییرات ماشینکاری در طول فرآیند طراحی ممکن است 100000 دلار هزینه داشته باشد، یا بازسازی قالب در مجموع ممکن است به 1.5 میلیون دلار برسد!
یکی دیگر از متخصصان گفت که کل فرآیند طراحی برای یک قالب فلزی بزرگ معمولاً حدود 4 میلیون دلار هزینه دارد. این امر توسط خودروسازان ممنوع تلقی شده است – به ویژه به این دلیل که یک طراحی ممکن است برای دستیابی به یک قالب کامل از منظر نویز و ارتعاش نیاز به دوجین تغییر یا بیشتر نیاز داشته باشد.
منابع گفتند، تناسب و پرداخت، ارگونومی و قابلیت تصادف از چالش های این طرح می باشد اما چشم انداز ماسک از ابتدا این بود که علیرغم خطرات، راهی پیدا کند تا زیر بدنه را به صورت یک تکه درآورد، برای غلبه بر موانع، تسلا به شرکت هایی روی آورد که با چاپگرهای سه بعدی از ماسه صنعتی قالب های آزمایشی می سازند.
با استفاده از یک فایل طراحی دیجیتال، پرینترهایی که به عنوان جت بایندر شناخته می شوند، یک ماده اتصال دهنده مایع را روی لایه نازکی از ماسه می گذارند و به تدریج قالبی را لایه به لایه می سازند که می تواند آلیاژهای مذاب ریخته گری شود. طبق نظر یک منبع، هزینه طراحی توسط ریخته گری شن و ماسه، فقط 3% درصد نسبت به کار با سایر روش ها ارزان تر است. این بدان معناست که تسلا می تواند نمونه های اولیه را هر چند بار که لازم است تغییر دهد و نمونه جدید را در عرض چند ساعت با استفاده از ماشین آلات شرکت ها چاپ کند. مانند Desktop Metal (DM.N) و واحد آن ExOne. دو تا از منابع گفتند چرخه اعتبارسنجی طراحی با استفاده از ریختهگری شن و ماسه فقط دو تا سه ماه طول میکشد، در حالی که برای نمونههای اولیه قالبهای فلزی از شش ماه تا یک سال طول میکشد.
آلیاژهای سفارشی
فریمهای فرعی زیر بدنه خودرو معمولاً برای کاهش وزن و بهبود قابلیت تصادف توخالی هستند.